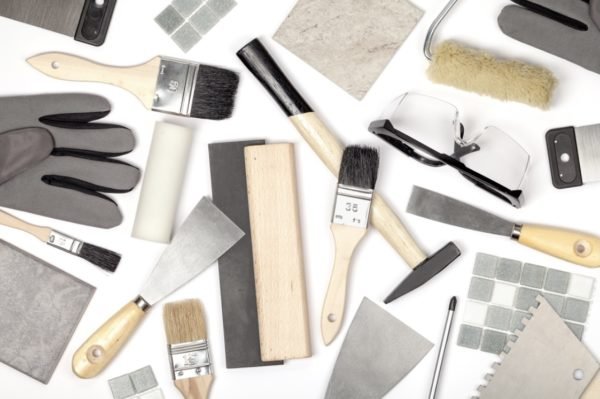
Tips for Buying Construction Equipment & Tools
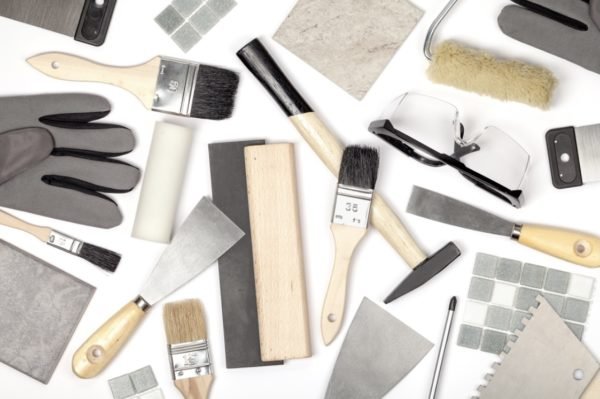
Buying construction equipment and tools for your jobsite is a huge responsibility.
Tools and equipment can cost hundreds or thousands of dollars. The quality of the equipment can also affect the safety of the construction crew and the quality of the finished project.
There are several factors to take into consideration during the buying process, such as which tools are required for the job, foreseeable jobsite conditions, your budget, the quality of the equipment and tools, and the level of hands-on experience you and the crew have with specialized tile tools and flooring equipment like scarifiers and scrabblers.
If you implement the following tips for buying construction equipment and tools that focus on these elements, you’ll be able to make cost-effective purchasing decisions that save you money but don’t cut down on quality.
Know Your Tools
Whether you are buying tools for the first time, buying tools for a new project, or replacing the equipment you currently use, a good place to start is to familiarize yourself with the tools and equipment used for the job. For example, if you routinely do tile work but have started taking on concrete work, you may have to do a bit of research to figure out what tools and equipment are essential for concrete jobs.
Depending on your project details, it is helpful to assess what tools and equipment the job requires, and then list what you already have. This allows you to see what you still need to purchase and prevents double buying or making costly last-minute purchases. Consulting a Repair Manual can be invaluable in understanding the specific needs of your equipment, offering detailed instructions and diagrams for efficient servicing and repairs.
Although there are many tools and equipment pieces required for different construction jobs, the following list presents a good starting point for different types of construction work.
● Tile and Stone
Tile and stone tools and supplies are necessary to lay tile in kitchens, bathrooms, and walls. Stone tools allow you to perform stone masonry for flooring, walls, and columns, depending on your project. Basic tile and stone supplies and equipment include:
○ Wet tile and stone saws
○ Spacers and wedges
○ Manual tile cutters
○ Tile drills
○ Trowels
○ Grouting tools
○ Adhesives for grout, mortar, tile, and stone
○ Polishing pads
○ Jackhammers and chisels
● Concrete and Masonry
Concrete tools allow you to break down surfaces for refinishing, mix cement and concrete, cut through concrete, and remove air from poured concrete so that it settles evenly. Basic equipment for masonry projects includes:
○ Cement and mortar mixers
○ Compaction equipment
○ Masonry saws
○ Concrete saws
○ Cut off saws
○ Concrete vibrators
○ Concrete floor grinders
○ Concrete pumps
○ Scarifiers and scabblers
● General Tools
General tools are items you’ll need for most job sites, including air filtration equipment and generators. You will also need to obtain OSHA-compliant safety equipment, such as face shields, glasses, earplugs, gloves, knee pads, and vests. Heavy equipment can be rented if you will only need it once or twice.
Safety equipment and safety clothing are there to help to reduce the risk of accident or injury to the worker and are important in every workplace. PPE is particularly important in the construction industry as the exposure to hazards is greater and the incidence of accidents more commonplace. Selecting the correct PPE (you can shop @ Unigloves for protective gloves) is essential to improve safety conditions in the workplace, for example, high visibility clothing allows the worker to be seen, workboots protect the feet and helmets protect the head from injury.
Consider Job Site Conditions
When buying equipment and tools, it is important to consider the conditions of your job site. This plays a major part in purchasing heavy-duty industrial equipment, as this type of machinery can be damaged by weather conditions or improper storage.
When considering the purchase of heavy-duty industrial equipment for your job site, it’s crucial to take into account the specific needs and conditions of your project. However, in some cases, it might be more practical to explore alternative options, such as renting equipment like a digger from Nationwide Digger Hire services. Renting heavy machinery can offer several advantages in scenarios where the equipment’s utilization may be temporary or project-specific.
Considering job site conditions like available storage and easy job site navigation are also important with mid-sized equipment and tools. Ensure you have adequate room and safe conditions to store a high-powered tile saw or scrubbing equipment.
For instance, storing saws or jackhammers at an industrial site may be permissible, but keeping equipment onsite in a client’s home may not.
Also, consider the size of your job site and whether or not it is safe to leave your equipment there. Each of these considerations allows you to make the best purchasing options for your project. It helps you decide on the size and power capacity of the equipment you buy and keeps you from making purchases that are not appropriate for the size and types of jobs that you take on.
Allocate Your Budget
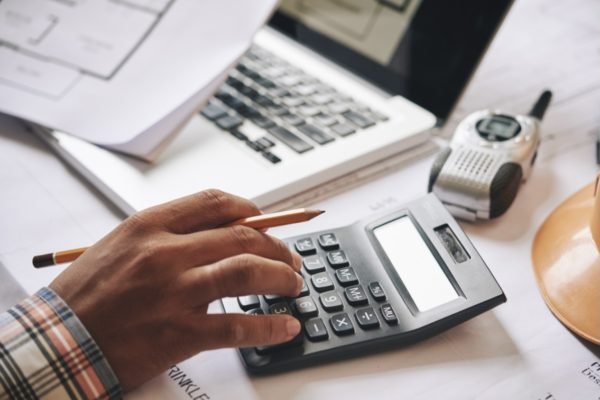
As a successful contractor, you are aware of the importance of budgeting your project. Some of the hard costs of a contractor’s budget are the equipment and tools needed for the job. One excellent tip for buying the necessary tools and equipment for a project is to ensure that your entire budget is planned out with realistic estimates of all costs, including labor, material, equipment, and supplies. With a realistic project budget, you can better assess how much you can spend on equipment, allowing you to decide whether or not it is a better investment to buy or rent larger-ticket items from crane hire or rigging services, or buy in bulk for smaller items like tile spacers or gloves.
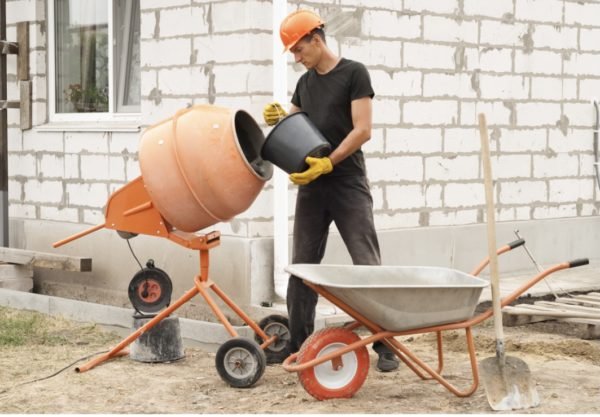
Assess Experience
When choosing the tools and equipment for your project, it is helpful to assess the experience of those who are working with you or who you are subcontracting to. While there are many complex tools with advanced features available, buying them when nobody on your team knows how to use them could be a wasteful decision. It is a good idea to obtain tools and equipment essential for the job and that your team knows how to use, rather than invest in power tools or technologies requiring specialized training.
Of course, training your team is vital to growing in the contracting business; however, when buying tools and equipment, especially when starting out, it is better to stick to the basics to save money until everyone gains experience.
Get Good-Quality Tools
Although it may be tempting to buy discounted or cheap tools, one vital tip about purchasing equipment is to always invest in good quality items at the start. High-quality tools and equipment cost a bit more upfront, but they last longer, perform better, and save you money in the long run. For instance, if you need a specialized Airport Low Profile Barricade for a construction project, buying them from a quality supplier will ensure they are better quality, with larger ballasting capacity so they can stand in the open without blowing away or being damaged.
Additionally, discount or cheap tools may not be made with quality materials or up to exacting specifications, which can put your crew at risk if they malfunction. They can result in subpar work or costly complications if materials are ruined and need to be replaced. Low-quality tools may also necessitate repairs and maintenance more frequently than better quality options.
Smart Purchasing Starts with Effective Planning
To make the most of your equipment and tool budget, assess your needs, buy quality items, and consider the conditions of the job site where you’ll be using your purchases.
By taking these actions, you can prevent overspending on low-quality tools that don’t last. Smart purchasing results from effective planning, so staying organized and knowing what you are looking for is the best approach to buying construction equipment and tools.